Share
Pin
Tweet
Send
Share
Send
De fato, esses são desenvolvimentos técnicos que não são tão difíceis e caros de serem feitos em casa com suas próprias mãos.
Uma dessas opções, baseada em um motor DC sem escova, queremos apresentar hoje. O autor propõe remontar esse motor da máquina de lavar roupa em um gerador, soldando novamente as bobinas principais do estator de maneira especial. Após esse retrabalho, o motor pode ser usado para uma turbina eólica. E se você equipá-lo com um dispositivo de entrada de água como uma turbina Pelton, poderá construir um gerador hidrelétrico.

Materiais e ferramentas necessários
Como você provavelmente já entendeu, hoje precisamos apenas do próprio motor da máquina de lavar. O autor usou um motor DC inversor da máquina de lavar americana Fisher & Paykel. Motores similares são usados em seus produtos pela LG, que está presente em nosso mercado doméstico.
Também precisaremos de:
- Ferro de solda, fluxo e solda;
- Cola quente;
- Lixa de grão fino - nulevka.
Ferramentas: alicate, alicate, faca de pintura.
Prossiga para remontar o mecanismo
Para a operação, será necessário desmontar o motor do corpo da máquina. Consiste em três partes principais:
- Estator - uma plataforma redonda com bobinas de enrolamento principais localizadas ao longo da borda externa do círculo;
- Rotor - uma cobertura de plástico ou metal com um núcleo de plástico. Ímãs permanentes são colocados ao redor do perímetro de sua parede interna;
- O eixo é a parte central do motor, equipada com rolamentos para transmitir energia cinética ao tambor da máquina de lavar.
Trabalharemos diretamente com o iniciador.

Preparação do estator
Colocamos a plataforma do motor em cima da mesa e começamos a trabalhar. Nosso objetivo é soldar as conexões de fase de acordo com um esquema diferente do original (foto).


Por conveniência, você pode marcar grupos de 3 bobinas com um marcador. Cortamos cada uma das 6 saídas das bobinas com cortadores de fio, de acordo com o esquema.


As bordas cortadas devem ser dobradas com uma chave de fenda ou manualmente, para que mais tarde seja mais conveniente trabalhar com elas.


Limpamos cada contato com uma lixa de grão fino para melhorar a adesão.


Quando tudo estiver pronto e limpo, conectamos todos os segundos grupos de três contatos. A torção manual é reforçada com um alicate.


Soldamos a torção com um ferro de solda usando um fluxo e a soldamos com solda de estanho. Desbloqueie a torção e solde-a pela parte de trás. Fazemos o mesmo com o restante dos contatos. Como resultado, devemos receber sete reviravoltas.



Loops de fase
Limpamos o grupo de contatos usado para fornecer energia ao motor.


Agora você precisa fazer um loop nas 3 fases restantes. Selecionamos o anel para a primeira fase. Nós fazemos isso a partir de um pedaço de cabo de cobre. Marcamos e cortamos no tamanho do círculo interno da plataforma.


Nós expomos o isolamento na junção com contatos livres e os removemos com uma lixa. Começamos a soldar o anel do grupo de contatos, passando cada um dos sete, terminamos com o último contato. Para conexões confiáveis, amarramos o final do contato no anel.




Nós rodamos a segunda e a terceira fases por analogia com a primeira. Deve-se tomar cuidado para não soldar os contatos adjacentes entre si.







Aplicação de isolamento
Nossa alteração do motor sob o gerador está pronta. Resta apenas isolar as aderências no anel e nas bobinas. Um método alternativo foi utilizado pelo inventor, usando cola quente como isolante.
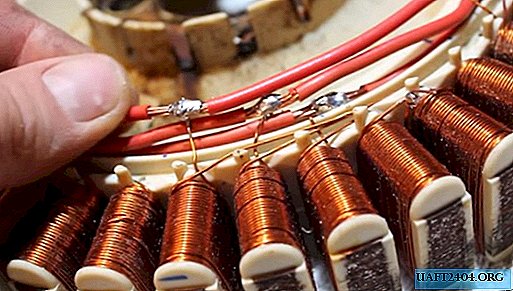

Segundo ele, esse isolamento nunca falhou. No entanto, para quem não tem certeza sobre esse método, vale a pena usar fita isolante. No final do trabalho, o motor é montado e pode ser usado no projeto pré-fabricado do grupo gerador.
Share
Pin
Tweet
Send
Share
Send